I finally tackled the problem on my boat that I have had since the boat was made. On my boat, the port exhaust leaves the turbocharger elbow and runs basically level across the back of the engine until it reaches an elbow/riser that dropped it down about 5 inches, and through the aft bulkhead, muffler and out the side exhaust. Being level like that I believe allowed seawater to enter the turbocharger, especially when rocking at anchor. This would explain having to rebuild the turbocharger once about ten years ago and replace it last year. That exhaust tube cleared the top of the hatch lifter motor by fractions of an inch. Besides the lifter motor, the sea strainer outlet was also just under the exhaust tube, again blocking any way to lower the tube. I had been looking for a solution for some time, and with some searching on the internet and contacting the manufacturer of the lift unit I was able to correct the problem.
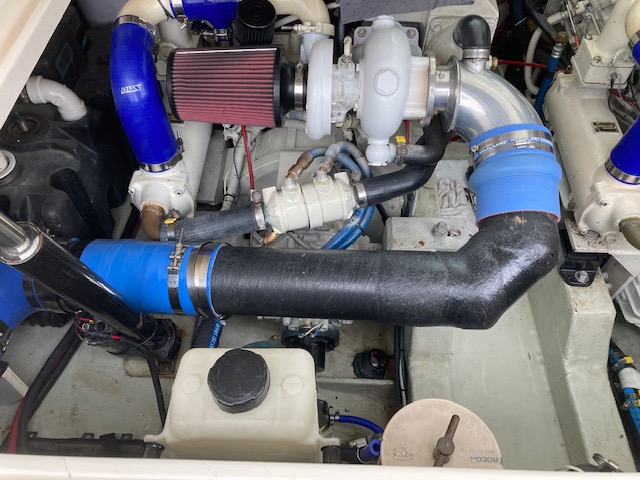
The first place to start was the hatch lift motor. The motor is mounted on the front of the lift mechanism and if it could be rotated to the side it would clear up the space needed for the project. I have seen them mounted with the motor down low as on my boat, and also up high, upside down. I did not want to mount them upside down for two reasons. Wiring could be a pain having to account for the travel of the hatch lifter itself, and I believe the lifter motor would still hit the exhaust tube.
I contacted the maker of the lift mechanism last year and was told that changing the orientation of the motor was not possible. I kept digging and found pictures online of similar units oriented as I needed, just not in marine applications. I e-mailed the service department at the same manufacturer explaining the issue I had with the exhaust system. I was told they could not say if it was possible or not (maybe product liabilities) but I did receive a link for a manual for the model I have. I looked over that manual many times checking the schematics and it sure looked like it was possible but it was not clear to me, so I kept digging some more. I did not want to take the engine room apart only to find it could not be done. I was actually prepared to cross drill the base of the lifter to make it work if needed. Over the winter I found a video online where a guy was taking one off a tractor step for repairs and it was the same model. In the video I saw the base removed and could see how the unit was made and how I could change the orientation of the motor. So, I started the project to lower the exhaust tube to get better flow of water out and help the turbocharger stay dry.
After removing the hatch lifter, I took it home and disassembled it on my workbench. The orientation can change in 30-degree increments. Just remember the top and bottom have to pivot in the same direction, they have to be oriented the same way. Once it was apart, I moved the lift motor 90 degrees toward the outboard side while keeping the top and bottom pivots parallel with each other. Once it was re-assembled, I installed it in the engine room to make sure it would clear the hull and any other gear that might be in the way of its travel. With that taken care of, I could move on.
My next problem was the sea strainer output fitting, directly beneath the exhaust tube, preventing any change to the exhaust system. With enough room aft of the strainer, I took apart the strainer and was able to rotate the sea strainer top 180 degrees to the rear. Using new gaskets and a new length of water hose I had the raw water supply reconnected in no time. Two down one to go.
Now I would be able to lower the exhaust tube from the turbocharger to the bulkhead, giving a nice drop away from the engine. I carefully cut the elbow/ riser out of the exhaust tube and installed a new silicone elbow there. This was a measure twice and cut once operation. Removing the elbow/riser left the exhaust tube a few inches shorter. To make up the few inches in length I used 5″ I.D. silicone exhaust hose that for some reason I had laying around in the wrapper for years, along with t-bolt hose clamps. It did take multiple test fittings to make sure it would all fit and still be lower than the original system but it all came together in the end.
The tube now drops about 4 inches from turbo to elbow and that should help a lot. I also made a support for the exhaust to keep the entire assembly from sagging. This is how it should have been done at the factory.
Next up is the starboard engine turbocharger. It is the original to the engine and is twenty-three years old. I have never had an issue with it but it is now showing a loss of boost pressure. I’ll replace all the engine and hull zincs during this time and have the bottom painted. The family gets the boat waxed for me as a Father’s Day present. Then, in the water we go!