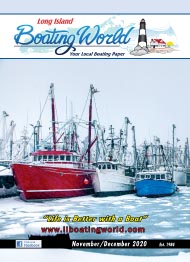
From the advent of submarine design, a crucial obstacle was the ability to provide life support for the crews and later-on combustion air for propulsion engines, hence, early submarines ran solely on batteries while submerged and so were considered to be electric boats. And although present-day nuclear-powered submarines can theoretically remain submerged and support life for many years, they still rely on a battery and a diesel generator as a backup to their nuclear reactors and their main propulsion and all systems operation are by means of electricity. This is why the company founded by the inventor of the first submarine sold to the U.S. Navy, John Philip Holland was named the Electric Boat Company and is currently owned and operated by General Dynamics Electric Boat Division that is still the primary contractor for U. S. Navy submarines.

During the earliest days’ modern submarines had to surface and open their hatches in order to recharge batteries and ventilate their internal atmosphere of stale and contaminated air and to replenish breathing air for the crews. This became an even more critical problem during the two World Wars because it left them vulnerable to enemy attack. However, during WWII a major breakthrough innovation was developed called the snorkel mast that allowed a submarine to come to periscope depth, raise its snorkel tube and draw in fresh air for the engines and to ventilate the atmosphere, and it allowed the sub to operate at periscope depth and run its diesel generators to recharge batteries while remaining hidden from the enemy and remain moderately safe from attack.
During World War II, diesel-electric comprised the majority of the propulsion systems utilized by the U.S. Navy for its submarines and although similar in design it was a departure from earlier submarines which were direct drive type systems where the diesel engine is directly coupled to the propeller shaft. In this configuration, located between the engine and the propeller shaft is a combination electric motor/generator (MG) set. And a clutch connects the engine to the motor/generator, and then a second clutch connects the MG to the propeller shaft. When the engine is connected to the MG it functions as a direct current (DC) generator and its output is directed through the switchboard with the switches selected to charge, and on into the batteries keeping them charged. Conversely, throwing the control switches to the battery position takes power from the batteries and directs it into the MG which then functions as a motor to drive the propeller shaft. Direct drive systems are limited because the narrow hull of a submarine precludes the use of more than two shafts. As a consequence, direct-drive subs were limited to one to two engines which were satisfactory for the relatively short-range designs of World War I and the inter-war period. And German submarines retained that system throughout the war in part because smaller submarines could be built in greater quantity, and the relatively small size of the Atlantic Ocean didn’t require extremely long range.
Subsequently, during WWII when the United States commenced the building of longer-range fleet submarines to operate both in the Atlantic and the Pacific Oceans it was concluded that more power was required since the boats were considerably larger with the Gato Class Attack submarines having a comparable length to a World War I destroyer therefore four engines were employed instead of only the preceding two. And so, the two-shaft configuration was still a limiting factor that presented a barrier to the transmission of power from the second pair of engines. Consequently, the solution was the introduction of full-time electric drive for the propeller shafts and by adapting a system originally developed for train engines where the diesel engines were directly coupled to a large direct current generator. This power could then be used for charging the batteries and/or powering the propulsion motors and, since there were four engines and generators, it was possible to use the full power output for the motors, and charging the batteries, or a combination of the two. Therefore, when the sub was submerged, the motors drew their power from the batteries. Some boats applied a reduction gear, and others drove the shaft directly off the electric motors. In the latter case, the motors were designed to run slower. The Gato Class boats had four electric motors, two per shaft.
Early USN Diesel-electric submarines were powered by one of three engine types at the beginning of WWII and one was the Hooven-Owens-Rentschler (H.O.R.), which was a license-built version of a German M.A.N. diesel that proved to be totally unreliable and so it was rumored that M.A.N. had deliberately provided faulty design specifications and drawings to the Navy, however, the Germans had poor results with the same engine design too. Ultimately, they were removed from all American boats and replaced with the more reliable H.O.R. engines that were a double-acting design in which a solid piston moves up and down within a double-ended cylinder which were common in applications for reciprocating steam engines of the time. But when applied to diesel engines it was an idea that proved better in theory than when applied in practice as H.O.R.’s double-acting engines gained notoriety for their unreliability in the submarine force where they were nicknamed “whores”. Owing to the limited space available within the submarines, either opposed-piston or, in this case, double-acting engines were favored for being more compact. However, an inherent problem with double-acting cylinders is the piston rod’s location slightly reduced the piston area on one side resulting in an imbalance in the force on each side of the piston. Therefore, H.O.R. engines were plagued by vibration and other problems as a result. This, in turn, overstressed the drive train and caused the gears, which themselves had been imperfectly manufactured, to shed cogs, create torsional vibration, and frequently rendered the engine and gear train completely inoperable. And, since the risk of engine failure could result in the deaths of an entire submarine crew the engines were scrapped. Eventually, two other more reliable designs were adopted, the 40° V-16 diesel built by Winton Motors Company, later acquired by General Motors Corporation and now commonly referred to as the “GM-Cleveland “because they were built at General Motors’ Cleveland Engine Plant, or just “GMs,” or a nine or ten cylinder 18 or 20 piston opposed-piston design built by Fairbanks-Morse which eventually became the standard for Cold war era USN submarines too. Most car enthusiasts are familiar with the one piston per cylinder design of gasoline automobile engines. Contrastingly, the Fairbanks-Morse engine operated on an opposed piston design that employed two pistons in each cylinder linked to two crankshafts. In that scenario, the tops of the upper and lower pistons meet at the midpoint of the vertical cylinder and their dished tops form the combustion chamber. This design effectively doubles the number of cylinders while keeping the engine comparatively compact.
The Gato Class submarines had two main batteries consisting of an assemblage of wet cells wired together in the battery compartment, one forward under the officers’ staterooms, and another aft below the largest crew berthing area. Each of these contained 126 wet cells with each cell being about 54 inches high, 15 inches deep, and 24 inches wide and they weighed about 1650 pounds or about 208 tons total for the two batteries. A byproduct of charging batteries is they produce hydrogen gas which is negligible in the case of a small battery in a car and where it is contained in a well-ventilated space but can present an explosive and environmental hazard in the case of a massive 126-cell battery within the sealed hull of a submarine. Therefore, battery compartments are ducted to a ventilation system intended to safely draw off the hydrogen and discharge it through the main exhaust mast while at scope depth or surfaced, and a means is also provided to seal off the battery compartments by isolating them from the atmosphere in the remainder of the boat. This is a safety feature and is particularly important in the event that salt-water seeps into the battery compartment since it can combine with the electrolyte to produce chlorine gas, a toxic gas that attacks the respiratory system, eyes, and skin. And because it is heavier than air, it accumulates at the bottom of poorly ventilated spaces. Too, Chlorine gas is a strong oxidizer and so may react with flammable materials. A battery well explosion and fire are one of the most dreaded emergency situations a submarine crew can face and it can spread fast, get out of control quickly and poison the internal atmosphere making it extremely difficult to combat. That was the exact case on 24 April 1988 while USS Bonefish SS-582 was submerged while conducting joint exercises off the Atlantic coast of Florida when seawater began seeping onto cables and electric buses in a battery-supply cableway resulting in arcing that sparked a battery compartment explosion and flashed into a fire within minutes raising the temperature in the battery space to 1,200° Fahrenheit. The heat was so intense that it melted the soles of the shoes of the crew members in the space above. So, the Captain ordered his crew to evacuate topside to await assistance, a luxury he may not have had in more hostile climate conditions or where rescue assistance was far more distant. The crews of a whaleboat deployed from nearby USS Carr FFG-52 and helicopters from both Carr and the aircraft carrier USS John F. Kennedy CV-67 rescued 89 Sailors. However tragically, three Bonefish crewmen died as a result of the fire. Afterward, naval authorities deemed the damage to Bonefish to be too expensive to warrant repair and thus deemed that she be decommissioned and scrapped.
Later built Gato Class fleet submarines were powered by four direct-current electric motors having motors powering each shaft. The motors and generators were furnished by General Electric, Westinghouse, Allis-Chalmers, and Elliot. GE and Westinghouse also built the main control units (switchboards), along with Cutler-Hammer. The application of a GE switchboard usually meant the boat would also have GE motors and generators. Westinghouse controls were used with their own motors and generators, or with the Elliott motors and generators. The Cutler-Hammer controls were generally linked with Allis-Chalmers motors and generators. Some indication of the amount of power consumed by these motors was the necessity to include water cooling systems to keep the operating temperatures within safe limits. The high-speed type motors used with a reduction gear were rated at 1370 horsepower and ran at 1300 rpm, pulling 2600 amps at 415 volts.
Located at the aft end of the maneuvering room, the main control unit consisted of multiple levers, indicator dials, and switches and the electrically-driven screws were controlled from this station and the “engine-room” engine order telegraphs were located there too.
Additionally, approximately 40 auxiliary motors of various capacities were located throughout the sub for the operation of compressors, blowers, pumps, hydraulic accumulators, pneumatic systems and other various equipment. Electric current for operation of these motors was supplied by the auxiliary generator, the main batteries, or a combination of both, through two auxiliary distribution switchboards. Therefore, all systems aboard were either directly or indirectly powered by electricity. The forward distribution switchboard, connected to the forward battery, fed all auxiliary machines in and forward of the control room, while the after-distribution switchboard, powered by the after battery or the auxiliary generator, fed all auxiliary machines aft of the control room. A bus-tie circuit connected the two switchboards, making it possible to feed one switchboard from the other in the event of an emergency.
The lighting system was composed of the ship’s service lighting system and the port and starboard emergency lighting systems; each was a separate distribution system. And power for the ship’s service lighting system on late type submarines was obtained from the batteries through two lighting feeder voltage regulators and a lighting distribution switchboard. On earlier ships, power for this system was supplied by lighting MG sets.
Diesel/electric propulsion remained the standard for USN submarines post-war and into the early years of the Cold war throughout most of the 1950s. The Barbel-class submarines were the last diesel-electric propulsion attack boats built by the United States Navy and they incorporated sweeping engineering improvements over previous classes. They were the first production submarines built with the modern day teardrop-shaped hull, the revolutionary design that was derived from extensive hydrodynamic and wind tunnel testing with an emphasis on underwater speed and maneuverability and that was first tested on the experimental USS Albacore AGSS-569, and they were the first to combine the control room, attack center, and conning tower in the same space within the hull. Additionally, they incorporated a double hull design with 1.5-inch thick HY80 steel. This class of submarine entered the Submarine Force’s fleet in 1959 and was taken out of service 1988–1990, leaving the Navy with an entirely nuclear-powered submarine fleet. Just three Barbel-class submarines were built; USS Barbel SS-580, USS Blueback SS-581, and USS Bonefish SS-582. The class overall essentially a smaller diesel-powered version of the Skipjack-class nuclear submarines, the first of which entered service only three months after Barbel, having been laid down only eleven days later. Several features of the experimental Albacore were used in the Barbel-class design, most notably the fully streamlined “teardrop” hull. Albacore’s single-shaft configuration, necessary to minimize drag and thus maximize speed, was also adopted for the Barbels, Skipjacks, and all subsequent USN nuclear submarines right up to current designs.